Unlocking the Potential: Testing the Robustness of ARINC 818 Protocol for Avionics
- r.foley
- Sep 18, 2023
- 2 min read
Testing, Simulating and Validating ARINC 818
Today’s Avionics video systems are pushing bandwidth demands to new limits. These higher bandwidth requirements are usually due to increased resolutions or frame rates of the video. ARINC 818 is an ideal candidate to handle mission-critical video requirements and thus has been gaining worldwide adoption in both military and civilian aircraft.
In ARINC 818, a system ICD (Interface Control Document) is required to define protocol parameters and timing parameters for the system. Testing ARINC 818 systems involves verifying protocol conformity as well as the timing of packets, lines, and video frames. Testing, simulating, and validating requirements fall under 3 broad categories based on application: Development testing, Production Acceptance Test Procedure (ATP) testing and Cockpit Simulators.
Development Testing

Development testing consists of protocol conformity and robustness testing. Conformity testing checks for errors within the protocol and ensures that ARINC 818 was properly implemented in a Unit Under Test (UUT). Avionics systems are low latency and therefore have no video frame buffers, only line FIFOs to handle video data. This requires precise line timing from transmitters so that the receivers always have the right amount of data at the right time. Robustness testing can check the receiver tolerance by varying the parameters of the incoming ARINC 818 stream. Inducing errors like CRC errors, 8B/10B errors, and OS errors can also help evaluate robustness and failure responses. Development testing ensures system reliability and sets the stage for a successful ATP.
Great River Technology’s (GRT’s) XF Tuner, and Video and Protocol Analyzer (VPA) (fig. 1) are excellent development testing tools that can be user configured to any ICD, and provide error injection/detection capabilities. They support almost any ICD on link rates up to 10 Gbps.
Production Acceptance Testing (ATP)
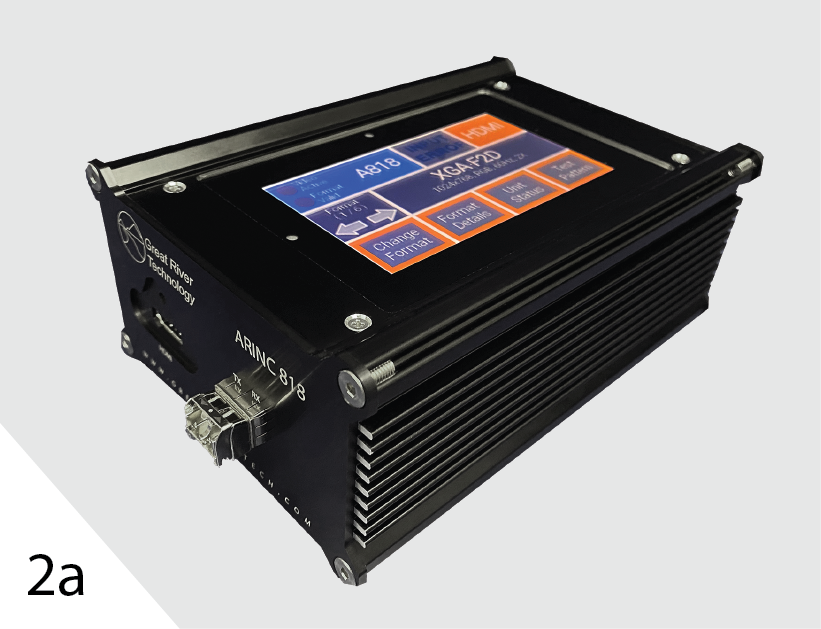
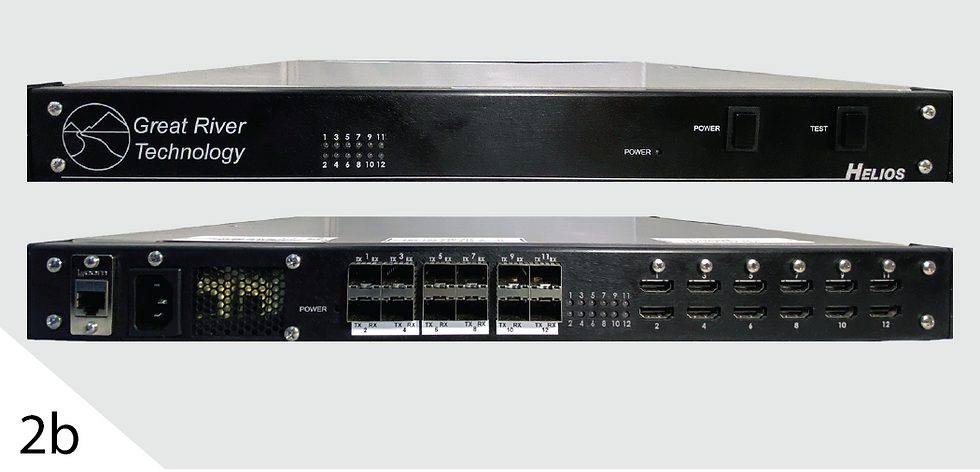
During ATP, simple ARINC 818 converters can be used to validate products since protocol and robustness testing is usually already done by production stage. GRT’s SAM G3 XI (fig. 2a) and Helios XI (fig. 2b) provide stand-alone and 19” rack mount solutions for production acceptance testing. When the application requires more than a simple converter, GRT’s Velocity XI offers a PC-based solution (fig. 3). An optional SDK allows the user to write their own application software. The ICD parameters for the SAM G3 XI, Helios XI, and Velocity XI are programmable in-field by the user.
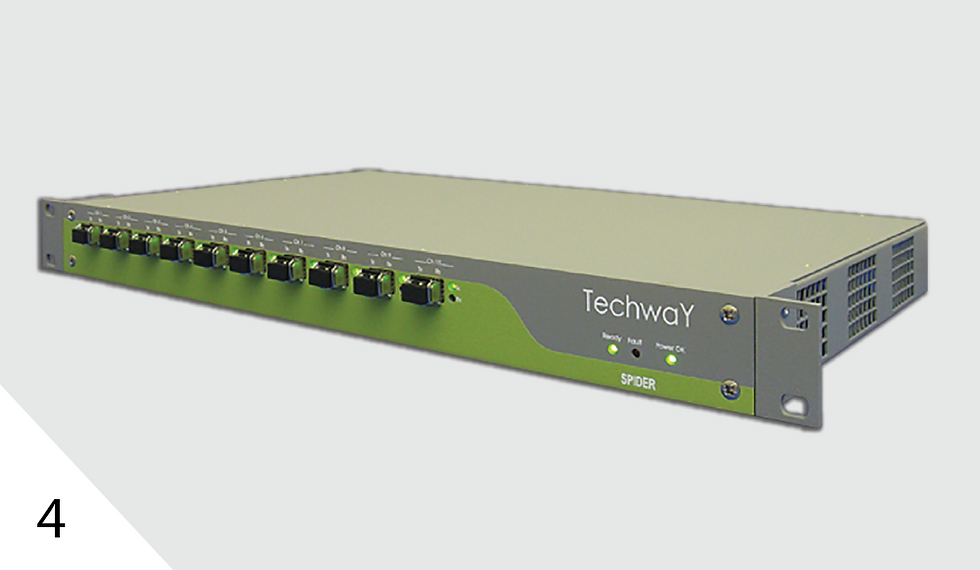
ARINC 818 switches can be used to reduce the number of ARINC 818 test devices required, keeping costs down. GRT offers the Techway Spider switch (fig. 4) with 10 channels that support link rates up to 6.375 Gbps. The Spider Switch’s broadcast mode allows users to replicate one input to any or all outputs.
Cockpit Simulator
ARINC 818 converters and switches can mitigate interoperability problems in cockpit simulators. Typically, cockpit simulators use commercial displays with standard interfaces like HDMI and DVI, which are not compatible with avionics systems. ARINC 818 convertors and switches can be used to configure cockpit simulators by efficiently converting and routing the video data between commercial displays and avionics systems.
GRT’s Helios and SAM G3 converters, and Spider Switches are used in cockpit simulators all over the world.